How to Cut Steel: 5 Different Methods Explained
August 6, 2024 | Categorized in: Production
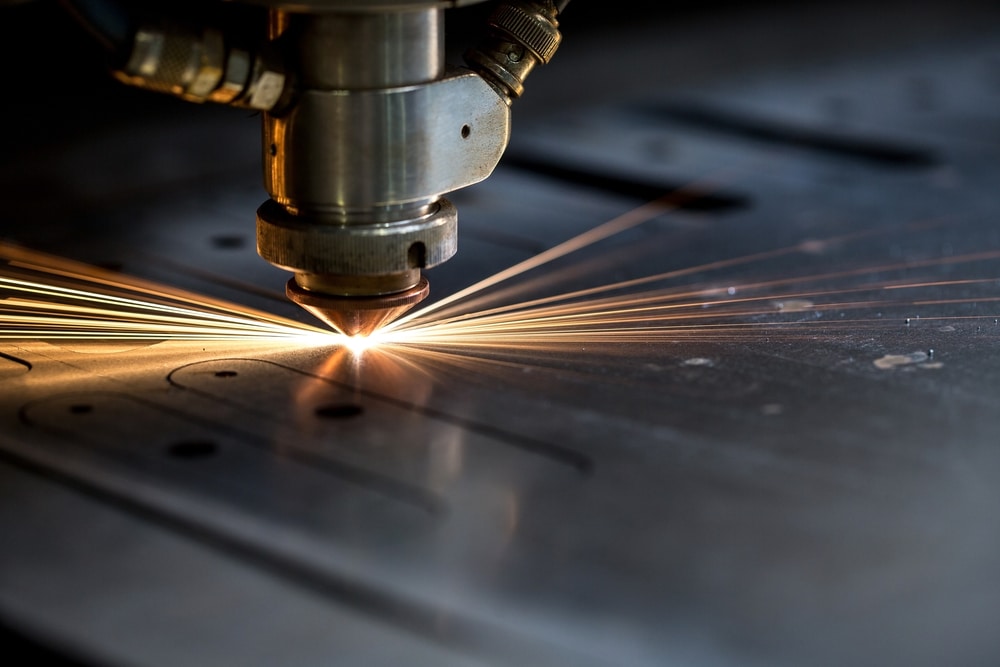
Steel cutting is a critical step in steel fabrication, but why does steel need to be cut after it’s produced and why are there different ways of cutting it? There are a number of factors that inform these decisions, so let’s go through them.
Why does steel need to be cut?
Steel products generally can be bought in standard sizes or dimensions, but many projects require different specifications for particular uses or situations. This is where steel cutting comes in handy and allows for even further modification and refinement of the steel you receive. For most projects using structural steel, raw steel arrives and undergoes precise cuts to transform into beams, plates, and pipes matching the final design. However, cutting steel can happen during multiple stages of a project:
- On-site construction often requires further cutting to fit steel elements together precisely or to accommodate existing structures.
- Unexpected situations or design changes may necessitate cutting for adjustments or repairs.
- Cuts are also crucial for preparing steel for connections, such as creating bevels for welding.
- Finally, demolition or renovation projects frequently involve strategically cutting and removing beams, tubing, and other steel shapes.
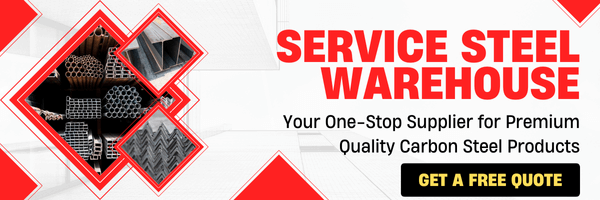
Best Ways to Cut Steel
Different methods might be used depending on certain aspects of the steel being cut and the tolerance or required precision of the cuts being made. The five primary methods used today are:
- Laser Cutting
- Waterjet Cutting
- Plasma Cutting
- Flame Cutting
- Production Sawing
Laser Cutting
Typically employed for thinner steel (less than 1.25 inches), laser cutting is highly accurate and minimizes material loss. It uses an intense beam of light focused by mirrors in the head of the laser cutter to direct the extreme heat at the steel and melt it along predetermined cutting paths. However, laser cutting is also slower than some of the other cutting methods and can heat the surrounding area of the cut, leading to warping or thermal stress.
Waterjet Cutting
As its name suggests, waterjet cutting uses high-pressure water (or a mixture of water and an abrasive substance, such as garnet or aluminum oxide) to erode and cut away steel quickly. Unlike laser cutting, there is no heat distortion from this method and it can cut thicker pieces of steel, up to 8 inches. Because of this, waterjet cutting is also the most expensive type of steel cutting due to its versatility, accuracy, and expensive operating costs.
Plasma Cutting
Plasma, or superheated ionized gas, is directed through a fine nozzle at steel (or other electrically conductive materials) and uses an electric arc that passes through the conductive plasma to melt the steel. The high-pressure gas from the nozzle then cuts through the molten steel and blows it away, cutting the workpiece. This method is quick, but is usually limited by a thickness of around 1.5 inches (2.5 inches for CNC plasma cutters) and can have a lower-quality cutting edge than other methods.
Flame Cutting
Also called oxy-fuel cutting, flame cutting steel often involves preheating the piece around the area that’s going to be cut. A torch is then used to combine oxygen and fuel gasses (acetylene, propane, propylene, etc.) to oxidize and melt the metal away, cutting through large steel products. While flame cutting is slower than plasma cutting due to the preheating process, it’s generally the most cost-effective method and can cut through steel as thick as 48 inches. Flame cutting can also be less finely tuned than other methods — but at these sizes, the accuracy and tolerances are much less delicate and strict. Most of the steel cutting that we perform is flame cutting.
Click Here to Learn More About Our Professional Flame Cutting Services
Sawing
The final method of cutting steel is also the most basic, and that’s using a circular shop or band saw for the process. Saw cutting steel can allow for close tolerances, as well as reducing the waste material produced. While not the most powerful method, it shines in situations where precision is key.
Depending on the size and shape of the metal being cut, most steel sawing will most likely use one of two types:
- Chop saws (pictured above) are most often used with abrasive cut-off wheels, are portable, and make quick cuts on various steel shapes like pipes and beams making them ideal for fast on-site cuts or for smaller steel sections. However, they can get hot and leave rougher cuts.
- Band saws (pictured above) use a continuous blade for a more controlled metal cutting environment which results in clean, straight cuts and minimal waste. Additionally, they can handle a wide range of thicknesses and can even follow a template for more intricate shapes.
Click Here to Learn More About Our Professional Steel Sawing Services
Cutting Steel: FAQs
How to Cut Steel Pipes?
Cutting steel pipes can be done using a variety of different methods. Mechanical methods such as sawing are common for smaller diameter pipes, providing clean, straight cuts. For larger or thicker pipes, an oxy-fuel torch can be effective, especially for quick and rough cuts. A plasma cutter is also a suitable choice, offering clean and precise cuts while being able to handle varying wall thicknesses efficiently without heat-induced warping.
How to Cut Thick Steel?
Thick steel requires robust metal cutting methods such as oxy-fuel flame cutting. This cost-effective method uses a high temperature from a flame to melt and oxidize the steel. Due to its speed and precision, plasma cutting is also effective for precisely and quickly cutting medium-thick steel (usually up to two inches).
How to Cut Galvanized Steel?
Cutting galvanized steel presents a unique challenge as it requires metal cutting methods that will minimize damage to the zinc coating and preserve its corrosion resistance. In these cases, mechanical steel cutting methods like sawing are preferred, since they don’t generate heat that would vaporize the zinc.
How to Cut Steel Plates?
Steel plates can be cut using a variety of methods depending on their thickness and the precision required. For thin to medium-thick plates, laser cutting is highly effective, offering high precision and clean edges. Plasma cutting is the most versatile as it can handle a wide range of thicknesses. For very thick plates, water jet cutting provides precise results without heat distortion.
Reach Out Today for a Custom Free Quote
Service Steel has the versatility to cut your steel products to size at a cost-effective rate and for any of your project’s needs. Whether you need flame cutting, sawing, or other finishing services such as galvanizing or impact testing, we can quickly supply you with the steel you need. Request a quote or give us a call today!
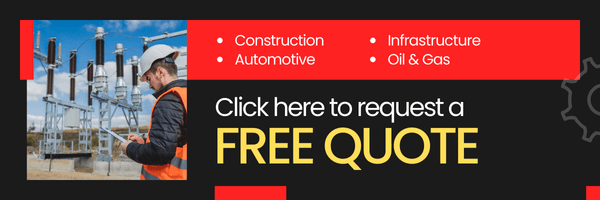