Guide to Charpy V-Notch Impact Tests
August 7, 2024 | Categorized in: Production
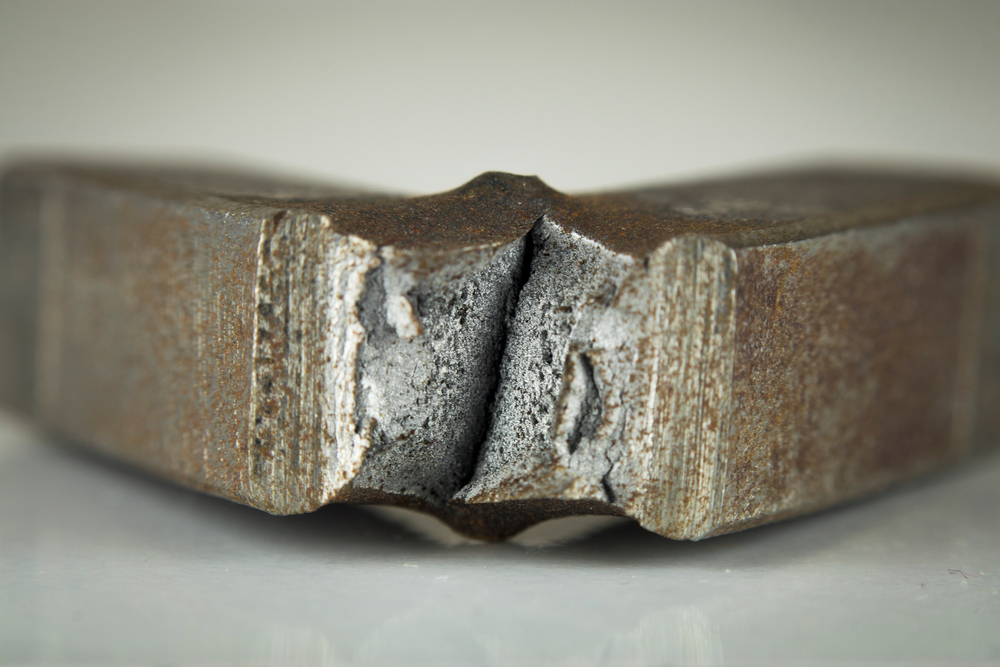
Charpy impact testing is an important test to ensure that your materials will perform in different conditions and environments, as well as the quality control process if specified by the end-user based on their project requirements. It can determine whether you’re able to use a certain component or type of part based on the applicable service temperature of the final build, but how is the actual test performed?
What is a Charpy impact test?
Charpy impact testing, or V-notch testing, is an evaluation of a material’s strength and performance under impact conditions. It involves a pendulum with a pointed hammer on the end swinging and hitting a machined piece of metal cooled to the required temperature to measure the amount of fracture at that temperature.
This is accomplished by setting the pendulum’s potential energy at a specified starting value. Once released, the hammer swings down and through the steel specimen and pauses at the height of its arc before swinging back. By measuring the potential energy at that pause and subtracting it from the potential energy before release, you can calculate how much energy the specimen absorbed or removed from the hammer’s swing, and therefore the material’s toughness.
History of the Charpy impact test
The history of Charpy V-notch impact testing dates back to the early 1900s when French engineer Georges Charpy developed a standardized method for testing the impact toughness of materials, particularly metals. His work led to the creation of the Charpy impact test, which involved striking a standardized specimen with a pendulum and measuring the energy absorbed during fracture. The introduction of the V-notch configuration in the 1940s further enhanced the sensitivity of the test to variations in material toughness, particularly for steel.
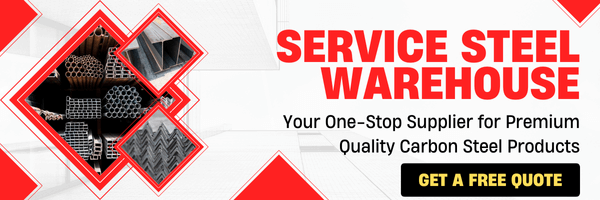
Why are Charpy tests important?
So why does it matter how much energy a small piece of steel can absorb from a swinging hammer? A Charpy impact test is crucial for analyzing the toughness of a material, and therefore important for ascertaining whether it can do a job or not. If you’re constructing the steel frame of a new building, you want to make sure the type of steel you’re using is strong enough to withstand the required conditions and temperatures.
Overall, Charpy V-notch testing is a valuable tool for quality assurance and materials selection in the steel industry, helping manufacturers ensure the performance, reliability, and safety of materials in a wide range of applications.
Applications of Charpy V-notch tests
Since its creation, Charpy V-notch testing has become widely adopted as a fundamental tool to test steel. Playing a crucial role in ensuring the safety and reliability of steel across various industries, including infrastructure, construction, automotive, as well as oil and gas. Some of the most common applications of this test include:
- Testing steel used in vehicles, such as suspension systems and crash structures, to evaluate crashworthiness and ensure compliance with safety standards.
- Evaluating the impact resistance of structural steel used in buildings, bridges, and other infrastructure, to ensure they can withstand different temperatures and environments without failing.
- Steel components used in heavy machinery benefit from Charpy V-notch tests as they test the suitability of steel materials and identify potential weaknesses that could lead to failure.
Charpy V-notch test: Step-by-step
To successfully perform a Charpy V-notch impact test, the following steps must be followed for accurate results:
1. Notch test specimens
The standard size of a specimen for Charpy impact testing is 10 mm × 10 mm × 55 mm. A 2mm deep notch with an angle of 45° and a tip radius of 0.25mm is then machined into one face of the bar. These specifications have a very tight tolerance because the shape and size of the notch can have a significant effect on the results of the test.
In addition, three specimens are usually produced and tested (often at a specified cold temperature), with an average of the three results being used as the calculated toughness of the material. There are other sizes (and a U-shaped notch) that may be used depending on the situation (such as 10 mm × 7.5 mm × 55 mm or 10 mm × 6.7 mm × 55 mm), but the standard dimensions cited above are usually what’s used.
2. Calibrate pendulum
Now that you have your steel specimens, it’s time to set the pendulum up for the test. This will vary depending on your Charpy testing equipment but often involves ensuring that the drag indicator reaches 0 when a test swing is done without a specimen.
3. Set pendulum
Once the hammer is calibrated, you need to raise it and lock it in place at the starting position. Double-check that the dial to record the height of the swing (and therefore the potential energy at that position) has also been reset and will record the measurements for this test.
4. Place specimen
Next, place the specimen horizontally in the anvil at the lower part of the machine with the notch facing away from the direction that the pendulum comes from. Line up the notch with the center of the channel that the hammer swings through (usually with a centering device on the machine).
If the specimens are being cooled for this test, this process needs to be done with time as a consideration. Removing them from the cold environment, placing them, and releasing the pendulum should take less than five seconds for each repetition of the test.
5. Release pendulum
Pulling a lever or switch releases the pendulum, swings downward, and hits the specimen at the bottom. Usually, the halves (or single deformed piece) of the steel will be thrown across the room or away from the machine so make sure you remember to pick them up afterward.
6. Report energy absorbed
Because the steel specimen will absorb a portion of the energy that the pendulum’s swing started with, it won’t reach the same height on the other side of the swing. Depending on your testing machine it will either record this on a dial or a digital screen, which you will then take note of and calculate the absorbed energy with. Some laboratories will calculate the energy absorbed for you on the dial or display that measures the height of the swing.
Steps 3 through 6 are then repeated for the other specimens before averaging the measured energy absorbed to come to a final result. Reported results will include information such as the temperature tested at, specimen grades, etc.
Ensure the strength of your steel today
We understand the importance of Charpy impact tests for steel and other services that are key to getting your project finished on time and with the highest quality materials. Always ensure your steel is suited to any environment and held to strict standards with Service Steel, providing fast, reliable, and excellent service for over 50 years.
Give us a call or request a quote today!
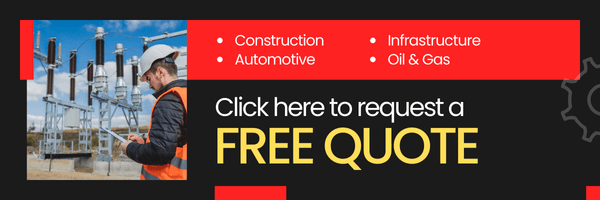